Hola a todos:
Después de unos meses por aquí sorbiendo conocimientos, ha llegado el momento de que de algo a cambio. Espero que a alguno le sirva.
En este mensaje describiré cómo realizo mis placas de circuitos. Hasta este momento solo he realizado tres, pero creo que ya lo tengo suficientemente depurado. Sobre todo teniendo en cuenta que la última tiene un tamaño de pista de 8 milésimas de pulgada y una separación entre pistas de 10 milésimas.
SOFTWARE DE DISEÑO DE PCBs
Ha este punto le he dado varias vueltas y he probado varios en los últimos meses (nunca había tocado uno, ya que la electrónica es una cosa nueva para mi, yo soy químico y he llegado a este mundillo por hobby).
Paquetes de software probados:
- CADSOFT Eagle
- Altium
- WinQcad
- KiCAD
Todos tienen sus pros y sus contras. Finalmente, me he decidido por KiCAD: ligero, rápido, con bastante soporte, aunque algo desperdigado, pero eficaz como el que más y, lo más importante, es software libre.
Podéis descargar la última versión estable desde aquí:
http://www.lis.inpg.fr/realise_au_lis/kicad/Y la versión de desarrollo compilada diariamente desde aquí:
kicad.1301.czLa placa que voy a utilizar como ejemplo es un adaptador de USB a IR, para conectar un multímetro Fluke que me van a regalar estas navidades (gracias, gracias) al PC. El circuito lo encontré en esta página:
http://users.tkk.fi/jwagner/fluke/En ella describen tanto una versión USB como otra para RS232. Desde ella me bajé el esquema y el diseño de PCB en formato Eagle. Copié el esquema con KiCAD:
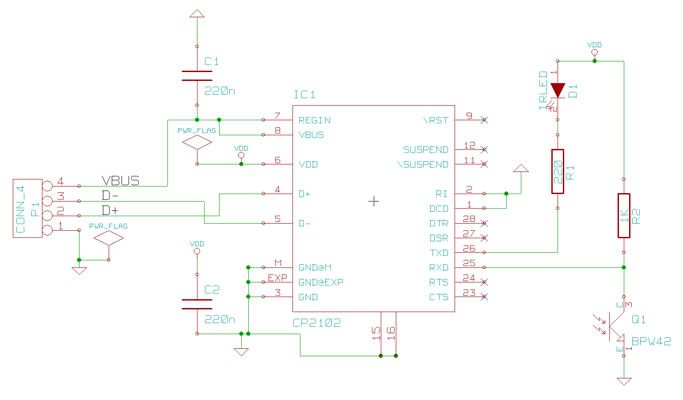
Y diseñé la placa:
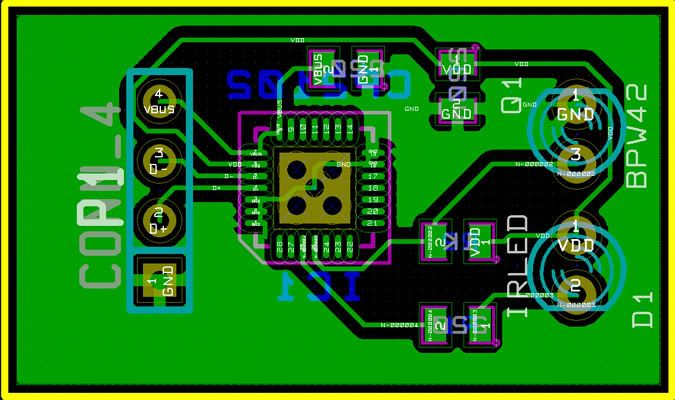
Con lo que pude preparar el fotolito:
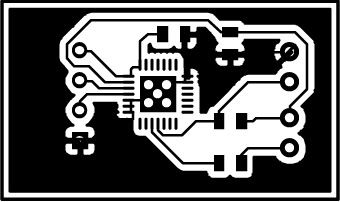
Aquí vemos el fotolito aumentado unas 10 veces, el tamaño real es de 2,92x1,75 centímetros. La anchura de las pistas reales es de 8 milésimas de pulgada (0,2032 mm) y la separación entre pistas de 10 milésimas (0,2540 mm).
INSOLACIÓN DE LA PLACA
El método de transferencia del fotolito a la placa puede hacerse de varios métodos, el más común es "el de la plancha" seguido del tradicional de insolación de placa sensible. A mi particularmente el de la planca no me atraía, aunque no puedo juzgarlo porque nunca lo he utilizado, me decidí por ir directamente al método de insolación, que tiene fama de ser el más preciso de los de "andar por casa".
En la red existen muchos diseños de insoladoras cada cual más desarrollado y con más artefactos y sistemas de cotrol. En mi caso, fui a por lo sencillo pero igual de práctico. Construí una insoladora para simple cara que se enciende y se apaga cualdo introduzco o saco el enchufe de la toma. Tecnología punta.
Para su construcción me basé en una pequeña cajonera comprada en Ikea. Se trata de una caja con tres cajones de aproximadamente 35x25x4 cm. Dos cajones para guardar el material de construcción de placas y el tercero para convertirlo en insoladora. Lo mejor de todo es que tras realizar la insolación basta meter el cajón-insoladora en su hueco y ya está recogido.
Mi insoladora:
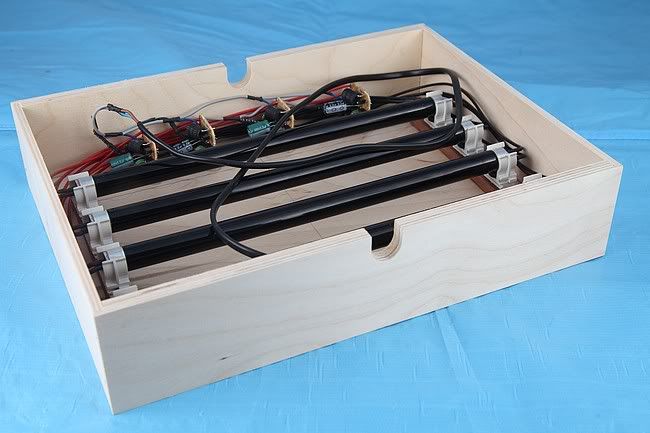
Vista general del cajón adaptado. Puede verse sobre los tubos el cable de alimentación.
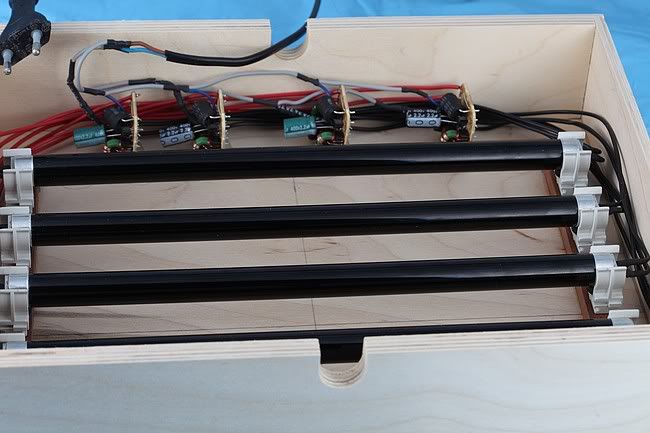
En el momento de su utilización el cable sale por una de las muescas que tiene el cajón y se conecta a la red. Estonces contamos: 1,2,3,4,...
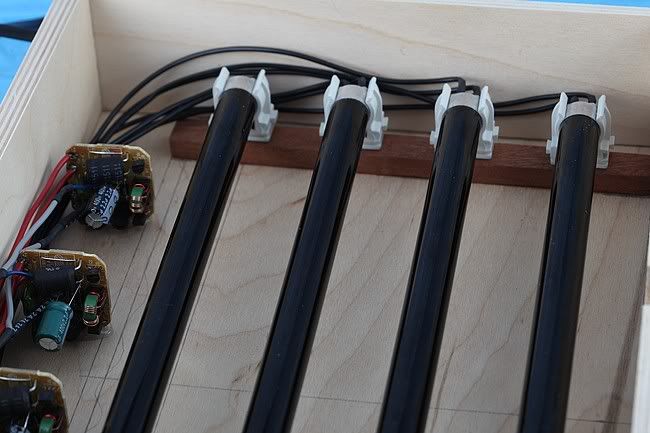
Los tubos fluorescentes UV van sujetos por medio de abrazaderas utilizadas para los tubos de cobre de conducción de agua potable. Éstas van atornilladas a un listón de madera pegado al fondo del cajón.
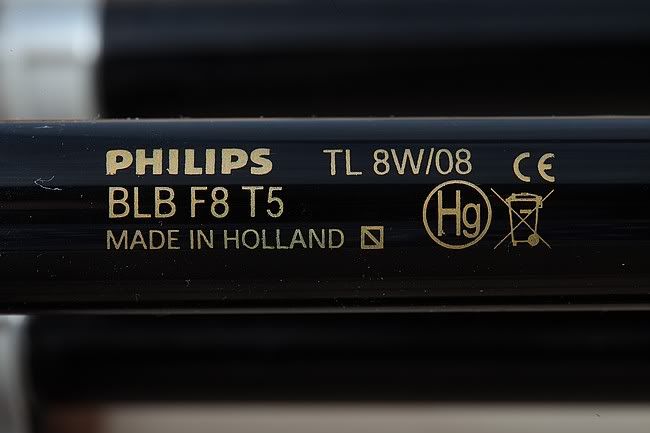
Referencia de los tubos utilizados. Lleva cuatro tubos de 28 cm.
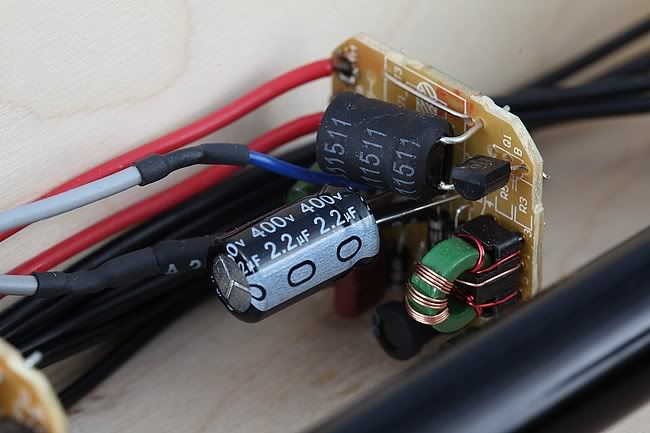
Para alimentar los tubos se recurre a circuitería electrónica. Nos evitamos el volumen, peso y calor generados por las tipicas reactancias. Cada bloque ha sido extraido de una bombilla de bajo consumo de potencia similar. Compré 4 bombillas de bajo consumo en una tienda típica de chinos. Son baratas y malas, pero la circuitería aguanta para estos menesteres. Cada circuito va pegado a la base del cajón con cola térmica.
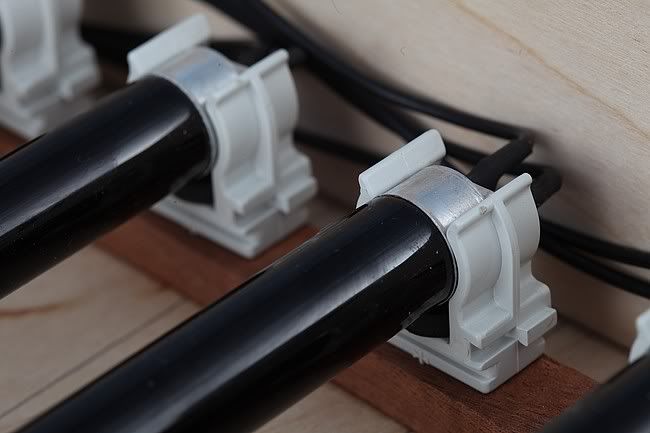
El cableado va soldado a la circuitería, pero los extremos van conectados a los tubos con terminales faston de tamaño adecuado, de forma que se hace muy sencillo cambiar un tubo si este se estropea.
Para utilizar la insoladora sigo los siguientes pasos:
- Coloco la insoladora-cajón en una superficie plana.
- Extraigo el cable de alimentación por el rebaje del cajón.
- Coloco un vidrio fino, proveniente de un cuadro de los de "clips", perfectamente limpio, encima de la insoladora.
- Coloco el fotolito sobre el cristal con la cara imprimida hacia arriba.
- Elimino la capa de protección y coloco la PCB virgen con la cara sensibilizada hacia abajo, perfectamente alineada con el fotolito.
- Coloco un pequeño peso sobre la placa, para ajustar su superficie con la del fotolito.
El fotolito lo imprimo con una impresora laser sobre papel de cebolla. Utilizo un solo fotolito, no duplico la impresión.
Para la placa positiva que utilizo actualmente (sin marca conocida), el tiempo óptimo de exposición es de 90 segundos. Realicé varias pruebas de exposición hasta encontrar en tiempo adecuado. Es importante resaltar que ese tiempo solo es válido para mi sistema de trabajo. Variará con cada insoladora y tipo de placa. Cuando compre un nuevo lote de placas deberé recalibrar el tiempo de exposición.
El tiempo de insolación es un factor delicado: poco tiempo y durante el revelado no se eliminará de forma suficiente la capa protectora; demasiado tiempo y toda la capa desaparecerá.
El sistema de control es el siguiente:
- Se introduce en enchufe en la toma, se cuenta hasta 90 y se saca el enchufe de la toma.

Es importante no mirar directamente a los tubos UV cuando estás encendidos, podrían dañar nuestros ojos. Es importante, son peligrosos.
El correcto manejo de la placa sensible conlleva, tanto antes como después de la insolación, que no se vea expuesta a los rayos del sol ni a luces potentes. Podemos manejarlas tranquilamente bajo la luz de una habitación los pocos segundos que tardaremos en insolarla y pasarla al revelador.
REVELADO DE LA PLACA INSOLADA
Como revelador utilizo una disolución de sosa caústica (NaOH) al 12%.
Este tipo de reveladores se comercializa en pequeños sobre o ya preparados para su utilización en tiendas del ramo de electrónica. Su precio es vergonzoso para su coste real. Lo prepararemos nosotros mismos. Basta con comprar una pequeña cantidad de sosa caústica (por aquí el precio ronda los 3 euros por kilo), digo poca por que con un kilo tendríamos para unos 83 litros, suficiente para "una temporada". Para la preparación de lo disolución de trabajo necesitaremos lo siguiente:
- Balanza o peso graduado.
- Cucharilla de plástico.
- Recipiente definitivo de 1 litro con un buen cierre.
- Guantes y gafas protectoras.
La sosa es un agente corrosivo de los más potentes que existen. Hay que protegerse bien en su manejo, las gafas y guantes son imprescindibles. En caso de entrar en contacto directo con ello, lavarse con abundante agua. Ésto significa poner la parte afectada bajo un chorro de agua durante unos 15 minutos. Sí, 15 minutos. Esto es así para cualquier parte del cuerpo, sobre todo los ojos. Es MUY IMPORTANTE aclarar durante 15 minutos.
Realizaremos todas las operaciones en un lugar muy ventilado y lejos de niños o animales que puedan derramar los preparados.
El método es sencillo: pesamos los 12 gramos de sosa y con la cucharilla de plástico la introducimos en la botella. Añadimops agua hasta unos 3/4 de litro, y agitamos hasta la completa disolución de la sosa. Despues, completamos la botella con agua hasta el litro.
La sosa desprende mucho calor al disolverse en agua. Para la pequeña cantidad con la que trabajaremos no es importante, pero para cantidades mayores, el calor desprendido puede ser tal, que nos quememos o que el recipiente plástico pueda ablandarse como un chicle. Atención a eso.
Para el revelado echo una pequeña cantidad del revelador preparado en un recipiente adecuado. Éste ha de ser de vidrio o plástico y con una base de diámetro ligeramente superior al tamaño de nuestra placa. Con echar hasta una altura de 5 o 6 milímetros de altura sobre el fondo de recipiente es suficiente.
Introducimos en él la placa recien insolada, con el cobre hacia arriba, y empezamos a contar, mientras agitamos suave pero constantemente, hasta el tiempo de revelado adecuado. En mi caso, y tras los ensayos pertinentes para mi tipo de placa, 60 segundos son lo adecuado.
De nuevo nos encontramos ante un factor decisivo: poco tiempo de revelado y no eliminares la capa protectora donde sea necesario; mucho y la perderemos toda.
Vaciamos el recipiente de revelado y enjuagamos en agua corriente la placa durante unos minutos. Durante este proceso de aclarado, yo froto la placa con los dedos, convenientemente protegidos por los guantes correspondientes, para eliminar la capa fotosensible que la sosa ha disuelto. De esta forma obtenemos una placa con el circuito perfectamente delineado y preparada para el ataque del cobre.
La sosa utilizada no se reutilizará. De esta forma el revelador siempre estará fresco y en óptimas condiciones y no nos llevaremos ninguna sorpresa al revelar. Es la forma de tener el proceso controlado.
ATAQUE DE LA PLACA
Aquí se nos presentan dos opciones típicas, el ataque con cloruro férrico (FeCl3) o con una mezcla de ácido clorhídrico (HCl) y agua oxigenada (H2O2).
El cloruro férrico lo descarté porque es un producto muy sucio y de procedimeinto lento.
De nuevo, protegeros con gafas y guantes ante4s de los procedimientos siguientes. La seguridad ante todo.
Para el atacador rápido basado en ácido clrhídrico y agua oxigenada necesitaremos:
- Ácido clorhídrico del 18%.
- Agua oxigenada de 110 volúmenes.
Para la preparación del ácido clorhídrico del 18% necesitaremos comprar ácido clorhídrico en alguna droguería o establecimiento similar. Nos lo venderán de una concentración aproximada del 30-33%.
Tomaremos una botella de plástico con buen cierre y añadiremos unos 550 ml de agua. Rellenaremos con el ácido del 30-33% hasta el litro y ya tendremos nuestra solución del 18% aproximadamente. Al manipular ácidos recordad que SIEMPRE se añade el ácido sobre el agua NUNCA el agua sobre el ácido. Recordad: EL sobre ELLA.
El agua oxigenada de 110 volúmenes es mucho más concentrada que el agua oxigenada utilizada para desinfectar eridas. La encontraremos el farmacias, droguerías e incluso en peluquerías, ya que suele utilizarse en la preparación de tintes. Su manipulación requiere la misma seguridad que la sosa o el ácido. NUNCA permitáis el contacto de vuestra piel con el agua oxigenada de 110 volúmenes, es muy oxidante y agresiva. ¡CUIDADO!
La solución de ácido clorhídrico del 18% y la de agua oxigenada no deben nunca mezclarse antes del momento de su utilización, ya que reaccionan.
Procedamos al ataque de la placa. De nuevo nos colocamos las debidas protecciones y nos preparamos en un local MUY ventilado.
En el mismo recipiente en el que hemos realizado el revelado, convenientemente aclarado con abundante agua añadimos lo siguiente y es este exacto orden:
- Dos partes de agua corriente.
- Una parte de ácido clorhídrico al 18%.
- Una parte de agua oxigenada de 110 volúmenes.
Las cantidades son relativas: dependen del tamaño de nuestra placa. Con que el nivel del atacador esté de 5 a 6 mm sobre el nivel de la placa es suficiente.
Agitamos suavemente el recipiente para que los componentes se mezclen bien.
AHORA, cuando tenemos el atacador perfectamente preparado, introducimos la placa en él, con el cobre hacia arriba. Durante el ataque agitaremos suave pero constantemente.
El tiempo de ataque no es tan decisivo como el de insolado o de revelado. Lo controlaremos visualmente.
Tras introducir la placa, el atacador comenzará, de forma progresiva, a eliminar el cobre expuesto. Esto conlleva la emisión de burbujas de hidrógeno: tendremos una PCB efervescente. El cobre disuelto pasa al líquido, tornándose éste de un color azulado. Según el cobre va desapareciendo, el burbujeo disminuye y podremos ver cláramente la superficie limpia de la PCB. Cuando veamos el circuito definido, sin cobre expuesto, podremos detener el ataque.
Para ello sacaremos la placa del atacador, con unas pinzas plásticas o similar, y la aclararemos abundantemente con agua.
Ahora podremos examinar atentamente la placa. Si vemos que aún quedan partes sin atacar, podemos introducirla de nuevo en el atacador sin ningún problema y continuar el ataque.
Una vez terminado el proceso, y con la placa perfectamente aclarada y seca, eliminamos la capa protectora de las pistas remanente con acetona.
En mi caso obtuve esto:

Placa terminada a tamaño real.
Vaaaaaale, que no se ve nada, os la amplio unas 10 veces:
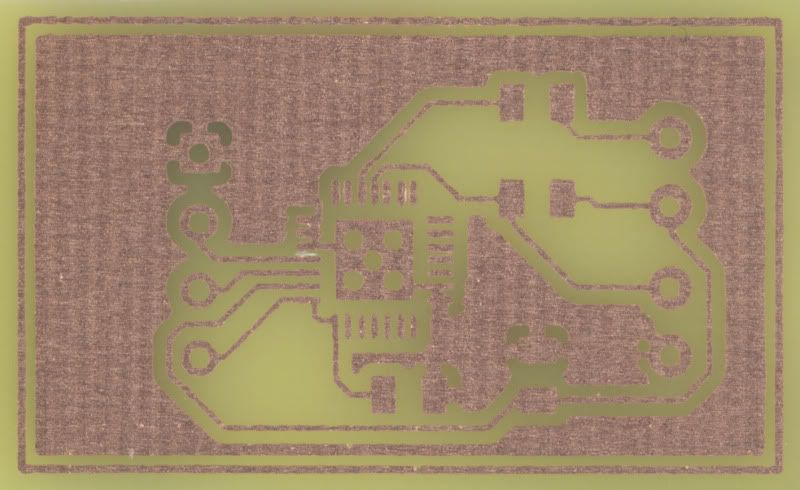
Para ser mi tercera placa y la primera con pistas menores de 25 milésimas de pulgada no está mal, ¿verdad?
SOLDANDO COMPONENTES SMT
Mis dos placas anteriores se utilizaron con componentes normales los llamados "through hole". Pero esta lleva tanto elementos tradicionales como SMD. Debo soldar a la placa los cuatro cablecitos internos de un cable USB normal y corriente, un LED IR y un fotodiodo IR. Chupado. Pero a ésto hay que añadir dos resistencias SMD, dos condensadores SMD y, la joya de la corona, un convertidor USB-USART de Silicon Labs CP2102, en formato QFN con ¡28! pines y un tamaño de ¡5x5 mm!. No había soldado en mi vida un componente SMD. A estudiar tocan. Me empapo de procedimeintos y videos por la red y me decido, voy a construirme un horno para SMT. Porque me lo merezco.

Tras darle unas vueltas al asunto, me decido a construirlo con un tostador de pan normal y corriente. Busco uno de forma adecuada que, por suerte, es el más barato del mercado. Tiene una potencia de 900W. Coste: 15,5€.
Lo desmonto, elimino carcasa y electrónica y obtengo esto:
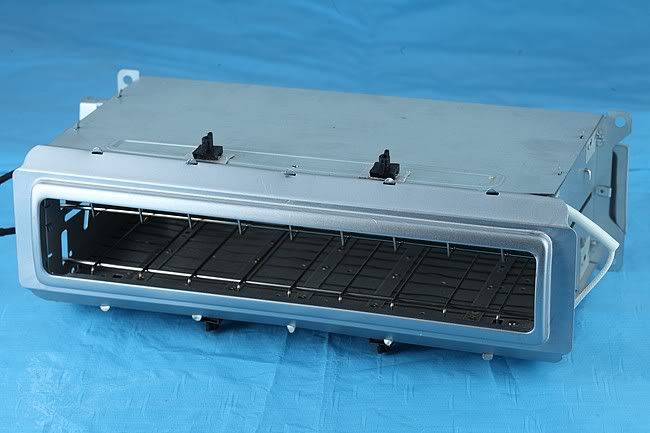
Aspecto esxterior del horno para soldar. Es apto para placas de hasta 14x25 cm.
El horno calienta uniformemente, ya que tiene una rejilla calefactora de NiCrom tanto en la parte superior como en la inferior.
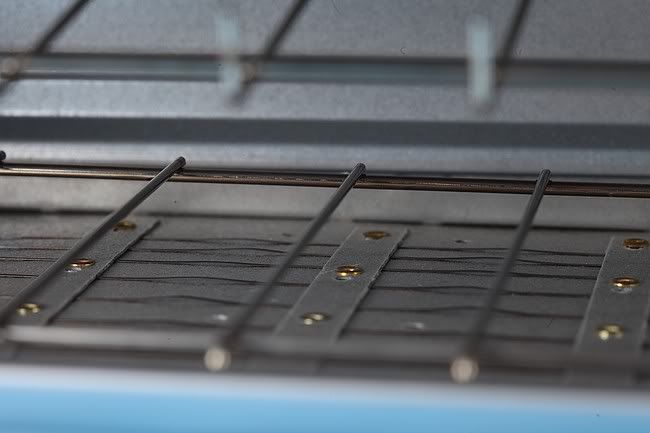
La rejilla interior que estaba diseñada para sujetar el pan es ideal para sujetar la PCB en su nuevo "trabajo".
La temperatura a la que debe trabajar el horno se controla mediante una sonda de Tipo K y un controlador de temperatura. El que dispongo solo admite un punto de consigna, por lo que he de intervenir en el proceso de soldado, no es completamente automático.
La soldadura de componentes SMD en horno conlleva un perfil de temperaturas adecuado. El proceso es más o menos el siguiente:
- Se ha de calentar el PCB desde temperatura ambiente hasta unos 150ºC de forma rápida.
- Se ha de calentar de 150ºC a 180ºC, poco a poco, durante un periodo de 60-90 segundos. En esta etapa los componentes eliminan su humedad y se atemperan.
- Se aumenta la temperatura hasta el punto de fusión de unos 220ºC de la forma más rápida posible, en unos 30 segundos y se apaga el horno.
- La temperatura de enfriamiento ha de ser gradual, de uin par de minutos. Generalmente basta con apagar el horno y esperar.
En mi caso concreto el proceso completo de soldadura con mi sistema es el siguiente:
- Aplico pasta de soldadura sobre los PADs. Es mejor andar justo con la cantidad que pasarse. Si se añade en exceso se formarán puente, que en componentes con patas puede eliminarse tras la soldadura con malla de cobre, pero en un QFN es imposible.
- Situo los componentes en su lugar, sobre la pasta. Una lupa y una buenas pinzas son imprescindibles.
- Coloco la placa en el horno. La pasta sujeta los componentes, pero los movimientos bruscos pueden desplazarlos de su lugar.
- Selecciono una temperatura de 180ºC en el controlador PID. Enciendo el horno.
- Al alcanzar los 150ºC cuento 90 segundos y subo el controlador a 230ºC.
- Al alcanzar los 190ºC cuento 60 segundos y apago el horno.
Este proceso me da un perfil de curva de calentamiento similar al indicado más arriba.
Tras dejar enfriar la placa completamente, sacamos el bollo del horno

Aquí lo tenemos:

Paca recién salida del horno.
Sí, sí, perdón:
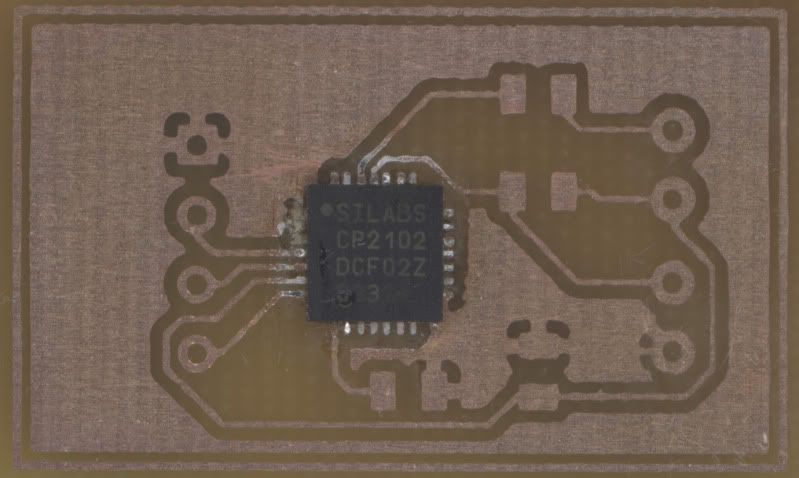
Imagen de la placa aumentada 10 veces.
Los manchurrones que se aprecian son debidos a los restos del fundente de la pasta de soldar. Se eliminan con alcohol isopropílico.
Como véis sólo hay un componente. Es debido a que aún no dispongo de las resistencias ni condensadores SMD. Además como era mi ptrimera placa y no sabía lo que podía ocurrir, me ahorré el taladrado previo.
Tras un cheque con el multímetro en busca de puentes, confirmo que la placa ha salido perfectamente, así que el próximo trabajo el hacer los taladros y soldar el cable USB y los LED. Cuando reciba los otros componentes SMD los soldaré a mano, que esos sí se dejan.
Esto es todo amigos. Siento el tostón. Si tenéis alguna duda o queréis más información sobre un punto en concreto, no dudéis en preguntar.